- Sustainability Report 2023-2024
- Environmental information
- Circular economy
Policies, targets and actions
The circular economy, as a true business enabler, is inherently part of ALPLA’s everyday operations. We are active in the four main aspects (the ‘ALPLA 4Rs’) of the circular economy relevant to our industry: we advise customers on lightweighting projects (‘reduce’); we develop refillable and reusable packaging solutions (‘reuse’); we continuously invest in mechanical recycling technologies following the bottle-to-bottle approach and provide design-for-recycling services to customers to enable recyclability in their respective products (‘recycle’); and we also conduct research and development on bio-based solutions and explore alternatives to non-plastic packaging options (‘replace’).
As part of ALPLA’s Sustainable Procurement Policy and the Supplier Code of Conduct, ALPLA employees and our upstream partners are committed to advancing the circular economy and sustainable sourcing. We require our key suppliers to contribute to our sustainability journey by taking action on decarbonisation and by maturing their sustainability management overall.
Since 2018, we have been a proud signatory of the Ellen MacArthur Foundation (EMF) Global Commitment programme, an initiative in collaboration with the United Nations Environment Programme (UNEP). Through this commitment, more than 500 organisations – including businesses and governments – have pledged to transform the way we produce, use and reuse plastics. Despite mandatory circular economy targets already being enforced in certain regions such as the EU, the US and India, our targets are voluntary, related mostly to our recycling activities and in line with the best practices of the Global Commitment programme:
By signing the EMF Global Commitment, we are actively driving the 4Rs of circular economy through various activities and joint actions. The following key products highlight our latest efforts related to the circular economy, highlighting our ultimate goal of ensuring that every product is designed with circularity and a small carbon footprint in mind.
Reduce
ALPLA promotes product lightweighting together with customers
- ALPLA Mexico has developed a 600 ml bottle made from up to 100% PCR for Coca-Cola, which is the lightest of its kind for highly carbonated beverages. The project, which took over four years, aims to enhance environmental sustainability by using lighter bottles with higher recycled content while maintaining high quality standards. The weight has been reduced by 12% since 2021 and by 45% since its original market launch in 2000.
- For the third ALPLA Sustainability Award in 2024, first place was awarded to the ‘wave bottle’ redesign in Steinabrückl, Austria, which achieved significant carbon reduction and cost savings through an innovative redesign. The 500 ml bottle’s weight was reduced by 18% while the 250 ml bottle’s weight was reduced by 20%.
- In 2023, ALPLA partnered with a customer to develop a new lightweight HDPE shampoo bottle. This innovative ‘roll and squeeze’ bottle is designed to help consumers use every last drop. It uses 45% less plastic compared to the original bottle and is fully recyclable as the entire system is made from monomaterial HDPE, including both the cap and the bottle.
Reuse
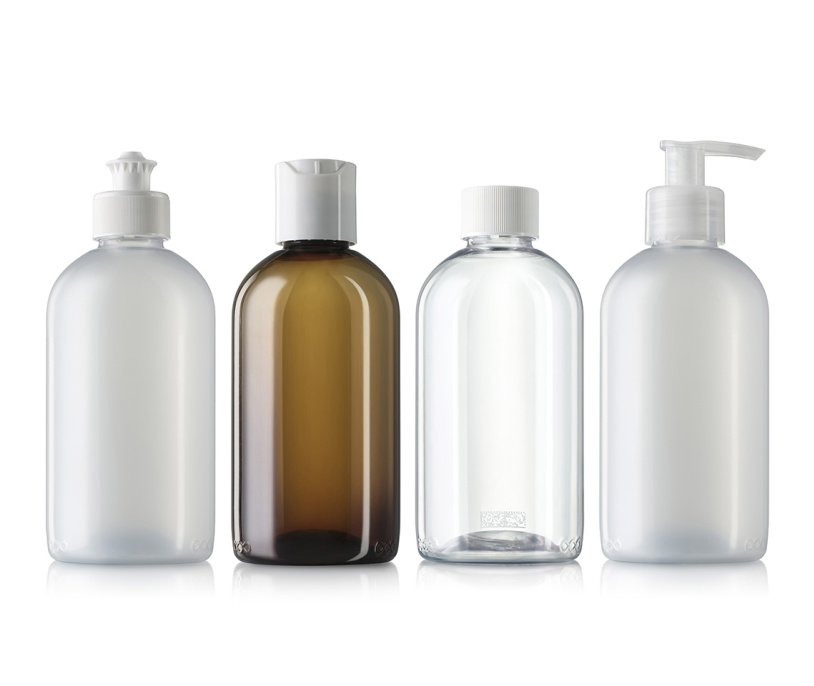
ALPLA, in collaboration with SEA ME GmbH, developed a reusable and fully recyclable PET bottle for cosmetics and care products.
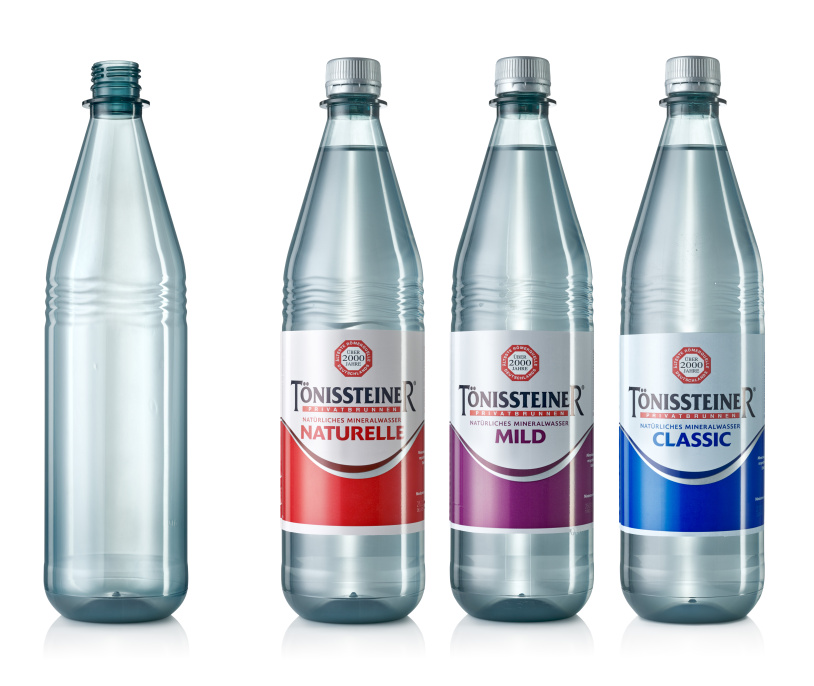
ALPLA and Tönissteiner launched the mineral water market’s first reusable PET bottle made of 100% PCR material.
Recycle
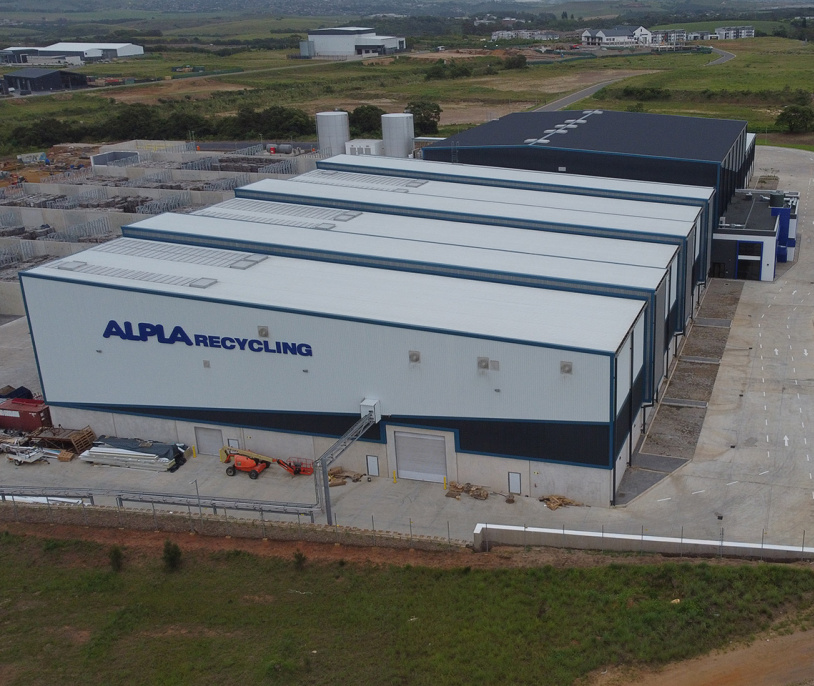
ALPLA opened a state-of-the art recycling plant in South Africa to supply up to 35,000 tonnes of recycled PET material per year from 2025 (2024).
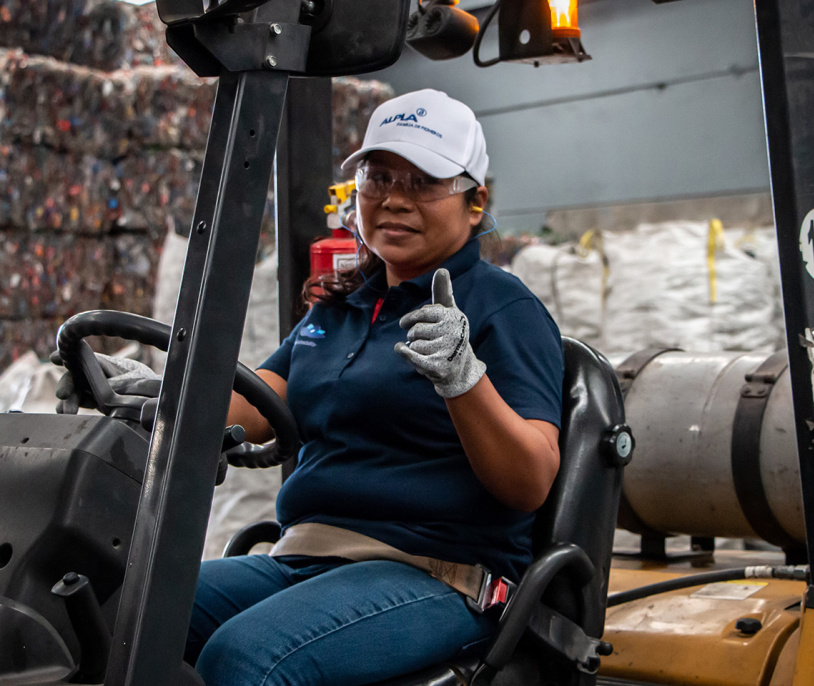
In Mexico, ALPLA partnered with IMER and PLANETA for plastic recycling while incentivising PET bottle collection to provide income for ‘socios acopiadores’ (waste collectors) and filling the gap in rural disposal facilities (2023).
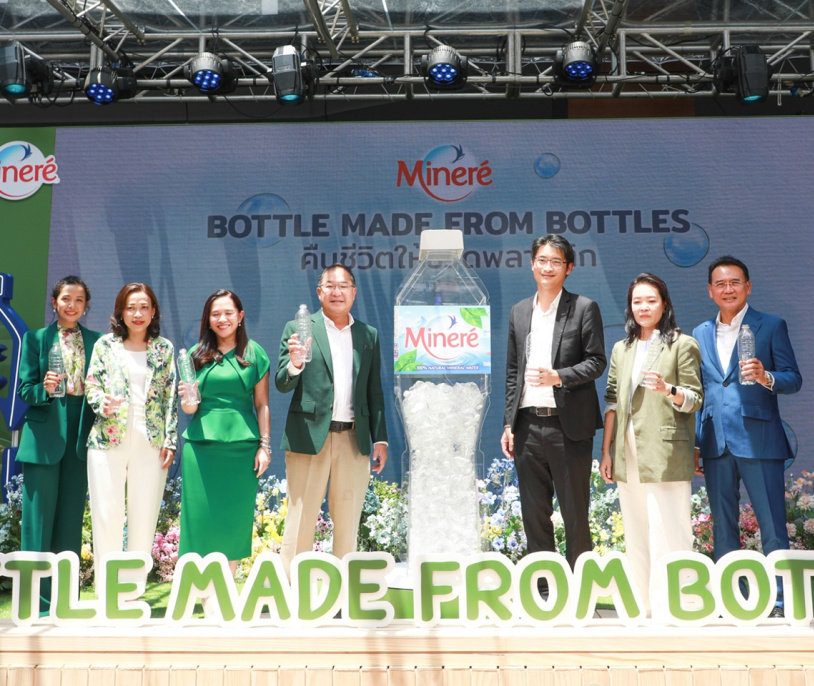
In Thailand, ALPLA and PTT Global Chemicals introduced Thailand’s first food-grade rPET to the market, featuring the first 100% rPET bottles for Pepsi and Mineré (2023).
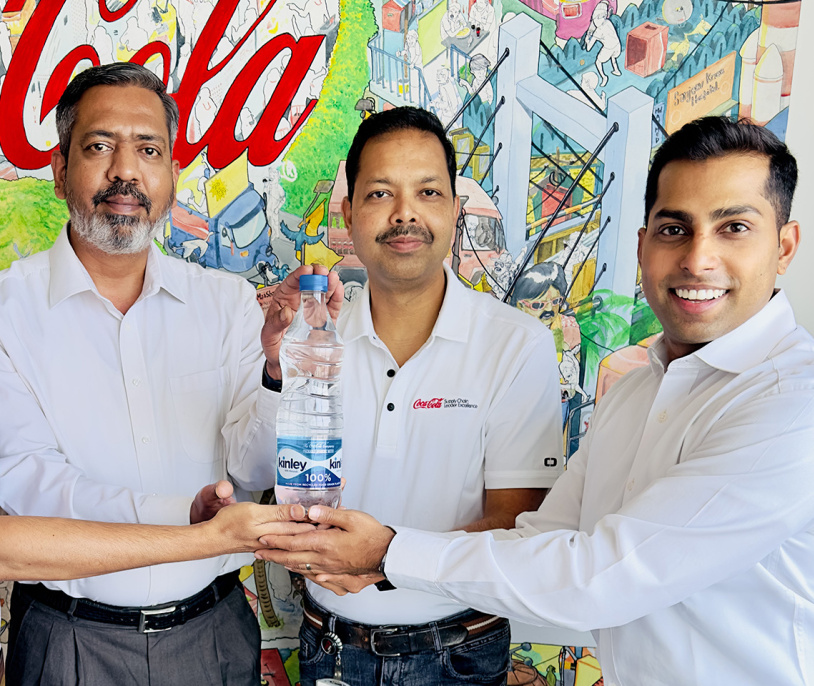
In India, ALPLA supported Coca-Cola’s launch of the first 100% rPET bottle, aiding Coca-Cola’s goal for 50% recycled material in packaging by 2030 (2023).
Replace
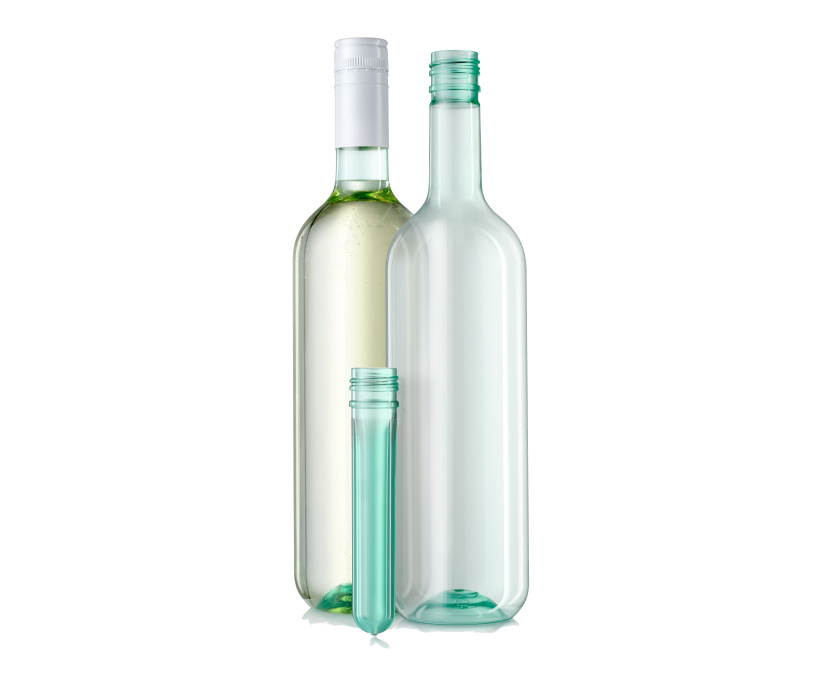
ALPLA launched a recyclable wine bottle made of PET, which reduces the carbon footprint by up to 50% and allows for price savings of up to 30% (2024).
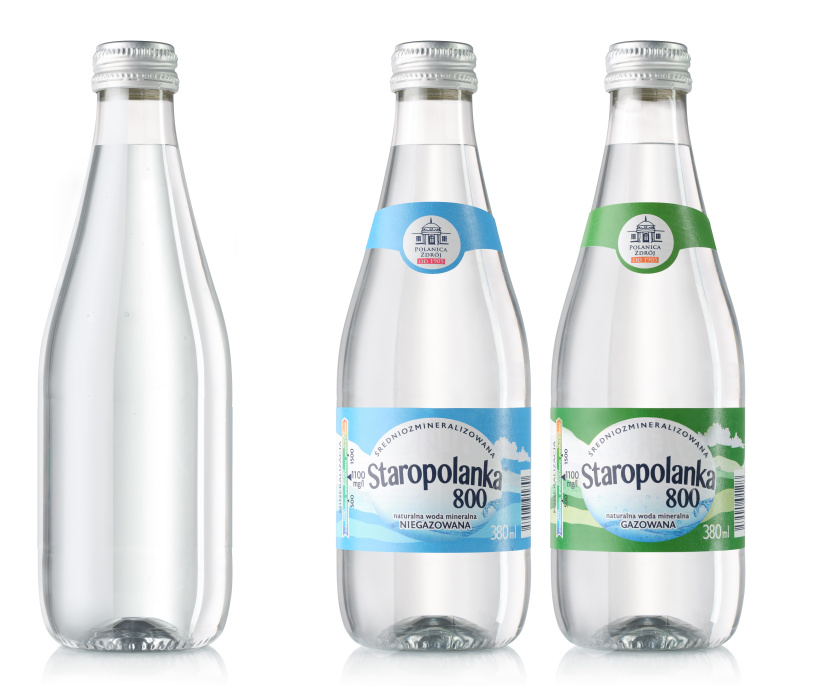
ALPLA developed a premium-look PET bottle for the Polish mineral water brands Staropolanka and Krystynka. This new bottle mimics the high-quality appearance of glass, is lighter, holds more water and is fully recyclable (2024).
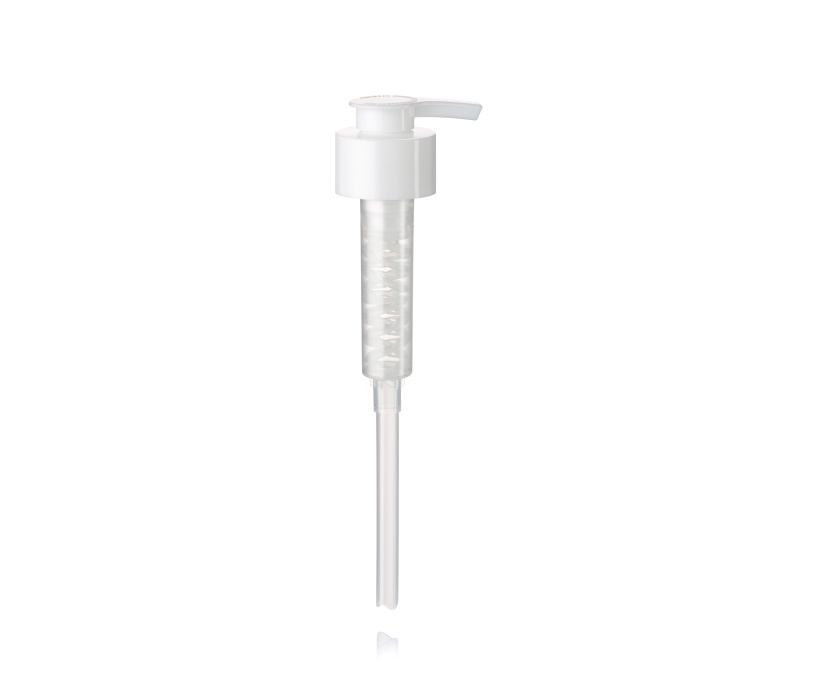
ALPLA’s joint venture in South Korea, ALPLAhana (since incorporated into ALPLAinject), developed a monomaterial dispenser pump with a down-lock function to create a fully recyclable and compact solution. It does not require a metal spring, needs fewer components and some of them can be made from PCR materials (2024).
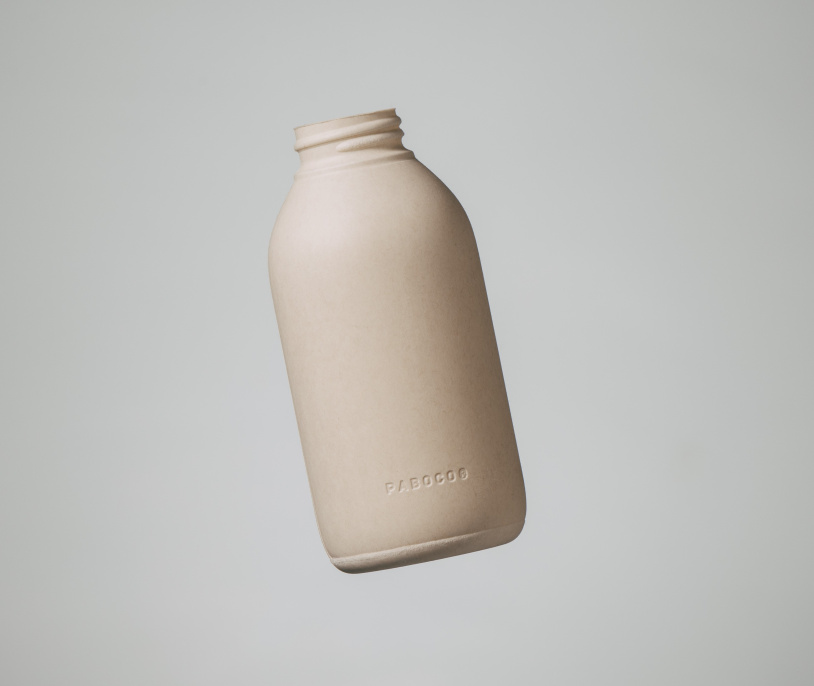
ALPLA took over the majority in its former joint venture Paboco and fostered the rapid market launch of the paper bottle with significant investment (2023).
Metrics
Material management
Our production predominantly utilises PET and HDPE, with PP being used to a lesser extent. The use of post-consumer recycled PET and HDPE is on the rise, driven by legislative requirements and growing customer demand. These recycled materials are – whenever feasible – sourced from our own recycling facilities. The use of organic materials remains infrequent due to the emerging nature of the technology and limited market availability as well as ALPLA’s clear focus on post-consumer recycled materials. We believe that while organic materials such as bio-based plastics play a crucial role in transitioning away from fossil-based plastic, their role should be to compete with fossil-based virgin materials rather than secondary materials.
Below we present the volume of our raw materials, based on purchase orders, including hard tolling and internal transfers of recycled raw materials. As depicted, our technical material usage has increased year on year while the usage of organic materials declined. Other purchased materials (including dyes and additives as well as secondary packaging used in production) account for only a negligible fraction compared to the raw materials, so we did not report these separately.
Recycled content share
Secondary (post-consumer recycled or PCR) materials are crucial from a circularity and a decarbonisation perspective. ALPLA is doing its share by operating a growing number of recycling plants in several countries while also purchasing recycled material externally in line with customer demand.
In 2024, ALPLA’s PCR share stood at 21.9%, representing a 1.8 percentage point increase on 2023 levels and nearly double the share recorded in 2020. Of the total PET used, 24.9% consisted of secondary material (rPET) while the share of recycled HDPE (rHDPE) relative to total HDPE usage stood at 21.1%. The gap between rHDPE and rPET has continued to decline, with the most recent reduction being 3 percentage points. When we study the rHDPE data further, we have seen PCR double in India and the AMET region and increase by 66% increase in the APAC region. For rPET, volumes more than doubled in India and increased by 50% in the NOAM region as well as 44% in the CEEU region. These increases in PCR are partially attributed to changing regulatory landscapes in these regions. For example, in India, the government has set mandatory PCR targets for rigid plastic packaging at 30% by 2025 and 40% by 2026, which explains the two-fold increase in PCR in that country. In the US, the rise in rPET could be driven by state-level PCR requirements, while the increase in rPET in CEEU can be associated with efforts towards the Single-Use Plastics Directive (SUPD) and the forthcoming Packaging and Packaging Waster Regulation (PPWR).
Recyclability
When calculating the recyclability of our products, we follow the guidelines of the EMF’s Global Commitment programme to assess components in two steps. First, we review the annual global recyclability assessment outcome by the EMF to determine whether a ‘system for recycling’ exists for key product categories defined by the EMF such as ‘PET bottles’, ‘HDPE bottles’, ‘HDPE other rigids’, ‘PP bottles’, and ‘PP other rigids’. Second, we assess the key product category of ALPLA’s product against the RecyClass design-for-recycling guidelines. Our assessment is limited to the products we manufacture, so components like labels and other accessories added by our customers are not considered.
In 2024, ALPLA’s global recyclability rate stood at 92%, representing a 1.2 percentage point decrease from 2023. We can associate this reduction to the fact that the total number of products manufactured and sold grew at a faster rate than the volume of recyclable products, thus increasing the overall denominator. Nevertheless, ALPLA is dedicated to developing strategies that enhance recycling and sorting potential, ensuring that all our packaging portfolio is fully recyclable in line with our target (100% recyclable products by 2025). This translates to close collaboration with our customers and supporting them on their journey towards circularity with a comprehensive approach applying the design-for-recycling principles in product development.
Waste
Our primary waste stream comes from our production process, specifically packaging waste such as plastic offcuts or defective products. These materials are typically reground and reused in production, effectively eliminating waste (and thus not reported as such).
Other waste streams presented in this Report include the following:
- other plastic waste that is not suitable for internal reuse
- metal waste (scrap metal from machinery maintenance and production equipment)
- chemical waste (residual chemicals from cleaning agents, solvents and lubricants used in machinery)
- secondary packaging waste (cardboard, paper, wood as well as plastic packaging materials used for transporting and handling products)
- electronic waste (obsolete or broken electronic components and equipment)
- organic waste (food waste from employee cafeterias and biodegradable materials used in some packaging)
- hazardous waste (batteries, fluorescent lamps and other materials that require special handling and disposal)
- textile waste (used protective clothing, gloves and other textiles from production processes)
In 2024, ALPLA generated a total of 105,000 tonnes of waste. As comprehensive internal waste reporting was only launched last year, 2024 marks our first year of comprehensive data collection. The reported data currently covers around 90 per cent of ALPLA’s operations, excluding some facilities such as newly integrated sites or those in regions where regulatory reporting requirements are still evolving.
Of the total amount of waste generated, 96% was non-hazardous. Both hazardous and non-hazardous waste types were predominantly directed to recovery, with 85% of non-hazardous waste and the majority (53%) of hazardous waste being recovered through reuse, recycling or other recovery processes. Approximately 87% of all waste in total was recovered, underscoring our commitment to circularity and resource efficiency.
Despite comprising a small fraction of industrial facilities within ALPLA, recycling plants were responsible for 47% of reported waste volumes. This high contribution partially stemmed from liquid waste produced during material recovery. Nevertheless, recovery remained strong with over 69.3% of waste being recycled in recycling plants.